Most wind turbine elements can be recycled
The first large quantities of wind turbines were commissioned in the late 1990s and early 2000s. Given their lifetime of 25 to 30 years, many of these turbines will reach the end of their lifespan in the second half of this decade and will be decommissioned. This makes the question of what to do with the huge number of valuable materials used to build them rather urgent. An increasing number of companies in the wind industry are actively looking into options for recycling wind turbines.
While 85% of a wind turbine can be recycled efficiently, the blades are still very difficult to recycle due to the materials used and their complex structure. One problem is the chemical properties of epoxy resin, a resilient coating substance used to strengthen the blades and long believed to be impossible to break down into reusable components. As it is almost impossible to separate the individual components, they must be processed together. This complicates the recycling process and the possibility of recovering residual value from the blades.
TPI Composites – Repurpose and recycle
TPI Composites (TPI) is a US company almost solely focused on producing blades for the onshore wind market, so it is at the forefront of the end-of-life recycling opportunity. The company produces blades for most of the large global wind turbine makers, including Vestas, GE, Nordex and Enercon.
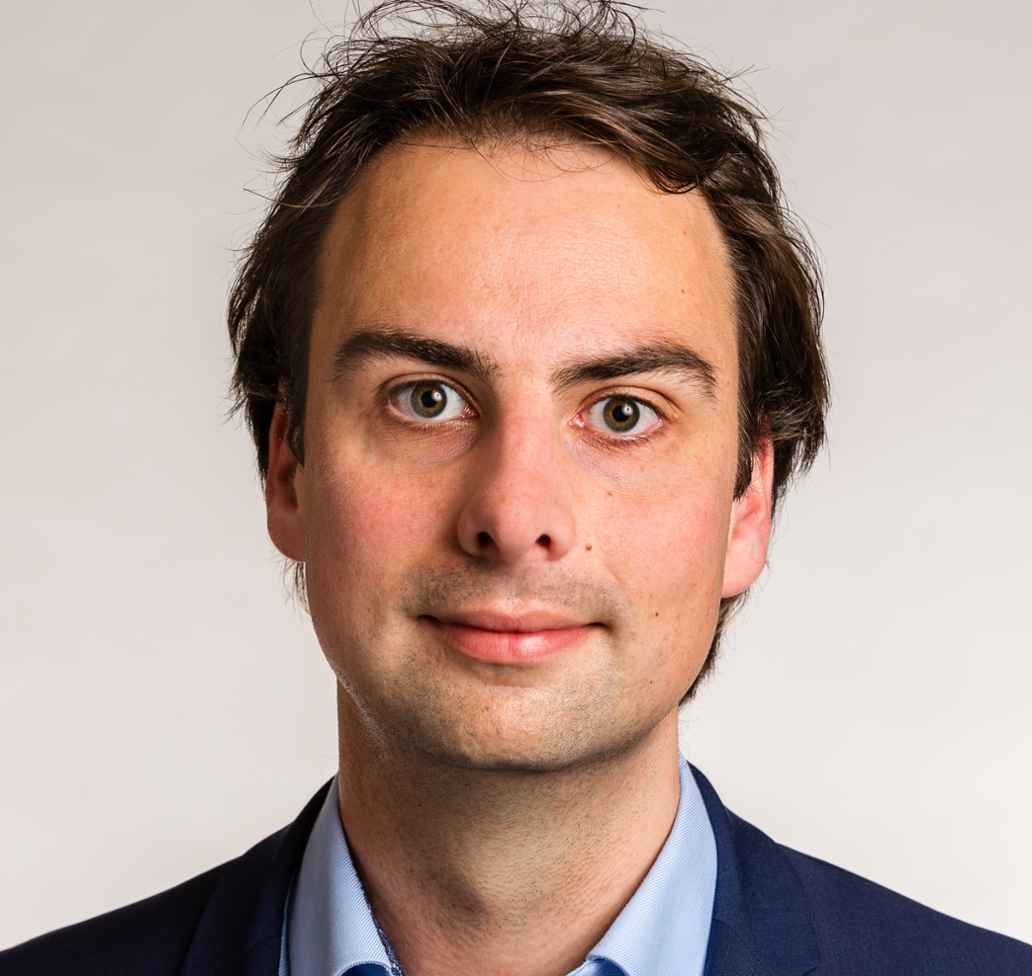
TPI is developing alternative uses for composite products reaching their end-of-life stage, leading numerous projects to find alternative uses for decommissioned wind blades, such as recycled fibreglass yarns, construction panels and structural flooring applications. In addition to repurposing end-of-life composite products, TPI works closely with industry and academic leaders to enable circularity for thermoset composites. This will allow for the recovery of high-quality composite materials such as glass fibre and carbon to be reused in building new wind blades or other thermoset composite products.
Vestas – Zero waste
Danish company Vestas (Triodos Global Equities Impact Fund and Triodos Impact Mixed Funds) is the largest western wind turbine producer. The company manufactures around 60% of its blades in house and outsources the rest.
Vestas is committed to creating zero-waste wind turbines by 2040. Through its Circularity Roadmap, the company has outlined a pathway towards this goal, which includes a commitment to create recyclable turbine blades. In 2022, Vestas recycled 475 end-of-life legacy blades.
Nordex – Full recyclability
Nordex is a German turbine manufacturer. The company manufactures about a third of its blades in-house. As part of its sustainability strategy, Nordex aims to produce fully recyclable blades by 2032. To this end, Nordex has already increased the number of fully recycled polyethylene terephthalate (PET) foams. It has reduced the use of balsa and polyvinyl chloride (PVC) foams, which prevents the emission of harmful gases when disposing of blade waste. In addition, Nordex is part of Horizon Europe, an almost EUR 100 billion EU framework programme which runs from 2021-2027. This initiative aims to stimulate science and innovation to tackle climate change and achieve the UN Sustainable Development Goals. Nordex is one of the partners in the European EoLO-HUB project “Wind turbine blades End-of-Life through Open HUBs for circular materials in sustainable business models”. In addition to end-of-life recycling, Nordex also aims to improve the service life of wind blades which is positive for economic and environmental durability. It uses a painted coating system to protect the blades from erosion and weathering. This reduces maintenance, increases efficiency and extends the blade lifetime.
ACCIONA Energía – From wind blade to solar panel
ACCIONA Energía is a Spanish renewable energy producer, generating both wind and solar power. As a utility, the company does not manufacture the equipment to generate power itself but purchases it from parties like Nordex. The company is responsible for the disassembly of wind turbines and solar panels at end-of-life, and along with the equipment manufacturers, it plays an active role in finding recycling solutions.
In 2022, ACCIONA Energía developed an innovative circular solution to use recycled material from wind turbine blades in the construction of new solar parks. By replacing steel frames with polymer frames to support the solar panels, recycled wind turbine materials get a second life so they can be used to generate clean energy again.
Solar panel recycling is in its infancy
Just like wind turbines, solar panels have an average lifespan of between 25 and 30 years. Currently, the recycling of solar panels at end-of-life is almost non-existent, as this market is still small and the infrastructure for scrapping and recycling them is lacking. The amount of scrap solar panels is expected to rise significantly however, highlighting the importance of developing an effective infrastructure. The International Renewable Energy Agency (IRENA) estimates a global amount of 4 million tonnes of scrap solar panels by 2030 and a staggering 200 million tonnes by 2050.
The difficulty with recycling solar panels is not that the materials they are made from are hard to recycle. Rather, it's that they are constructed from many parts all used together in one product. Separating these materials and recycling them individually is a complex and expensive process. Like the turbine owner, the panel owner is responsible for processing the solar panels at end-of-life. Panel manufacturers play an important role in designing panels for easier and efficient end-of-life recycling process, optimising the material recovery rate.
First Solar – First in recycling solar PV
First Solar is a US company producing solar panels for the utility-scale market.
First Solar is currently the only panel manufacturer with global in-house photovoltaic (PV) recycling capabilities. While most PV recycling processes focus only on recovering high-mass materials such as glass and frames (i.e. bulk recycling), First Solar’s process also allows for the recovery of so-called closed-loop semiconductors for use in new modules. First Solar converts mining by-products into a leading eco-efficient PV technology using less energy, water and semiconductor materials than other PV technologies. This maximises material recovery at end-of-life. According to First Solar, this will result in the recovery of more than 90% of module materials for reuse, providing high-quality secondary resources for new solar panels, glass, rubber and aluminium products.
Making the renewable energy sector fit for the future
We will soon face the retirement of first- and second-generation wind turbines and solar panels, while the number of new installations will continue to grow. The use of scarce materials and the amount of waste will consequently also increase. A successful energy transition requires a renewable energy sector that is also sustainable. Driving the generation of renewable energy through wind and solar is essential but must go hand in hand with enhancing resource efficiency. Recycling is therefore a critical next step in the development of the renewable energy sector. Several companies in the wind and solar industries are actively developing solutions to recycle the valuable materials used in turbines and panels. As impact investors, we must support them and at the same time stimulate others to do the same.